Abrasive blast media types and their uses
Wet blasting or vapor blasting is a highly controllable finishing process that allows users to achieve a precise finish on their components.
One of the many controllable variables in the wet blasting process is the blast media.
It is important to understand what different types of abrasive blast media are available and the finishes they can produce because they have a major effect on the wet blast process and ultimately the finish applied to the surface in question.
An abrasive blast media, by definition, are the particles of solid material that cause abrasion and erosion when impacted onto a target material, and there are a lot to choose from!
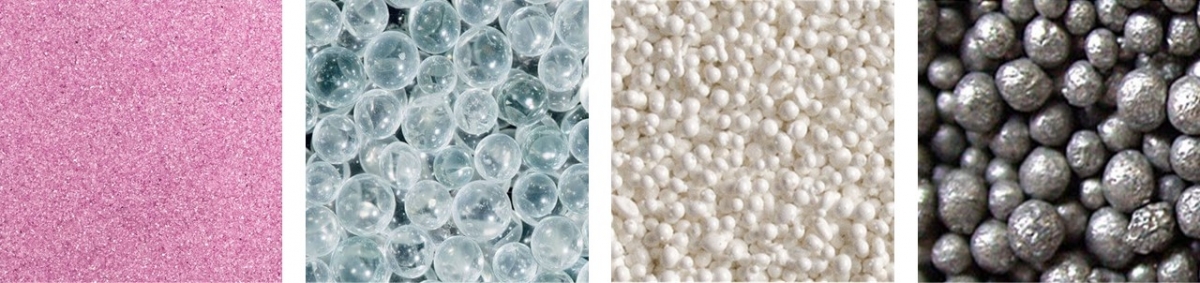
Aluminium Oxide, Glass Beads, Ceramic Beads, Stainless Steel Shot (Note: Media particles are not in scale to one another)
Here are some of them and their benefits.
Aluminium oxide
- Aluminium oxide has a relatively aggressive cutting action that is capable of removing tough coatings and contaminants from hard metals. It is a great media for heavy applications where parts require a lot of cleaning.
- Aluminium oxide is usually the blast media we recommend when a specific roughness is required.
- It is commonly available in three different colours, white, brown and pink. White is the sharpest, but most friable (breakable), it is purer than the others and has no iron content. Brown is toughest and is blunt in comparison, it is usually re-claimed and can look grey in colour too. Pink is a compromise between white and brown.
- It is frequently used for surface preparation in aerospace and other industries with demanding requirements.
Glass
- Glass beads create a consistent smooth and uniform surface finish, making them suitable for applications where aesthetics are crucial. The media is often used for polishing or satin finishing parts. Being spherical in nature the media produces a smoother finish than aluminium oxide.
- They can be made from normal soda glass, or from toughened glass ‘engineered beads.’
- New beads are often coated in silicone to stop them from clumping together in the bag, however, beware, this can make fine beads float! There is also a risk of contamination which will seriously impede bonding.
- It is an ideal media for cleaning and deburring delicate materials without altering their dimensions or causing surface damage.
- Glass beads can also produce a peening effect on surfaces.
Garnet
- Garnet has a moderate cutting action providing effective cleaning and surface preparation without causing excessive damage to substrates.
- It can be used on a wide range of surfaces including metals and composites, making it versatile for various applications.
- Garnet can be recycled and reused multiple times, reducing waste and operating costs.
Silicon carbide
- Silicon carbide has an aggressive cutting ability that is highly effective in removing stubborn coatings and rust from metals.
- It can produce a non-reflective, matte surface on metals and is often used in automotive and decorative applications.
Plastic media
- Plastic media offers gentle cleaning and deburring without causing damage to softer materials.
- Traditionally made from recycled plastics such as bottles, buttons, cutlery etc., when used for wet blasting it can remove paint or surface contaminants such as fat or grease.
- Being softer than metal, plastic media can be used to clean parts without affecting the underlying substrate.
- When using the media to remove paint, harder plastics can be used to remove harder paints and it is also possible to remove a top layer of paint while leaving the underlying primer layer of paint in place.
- It can be made of several base materials like melamine, acrylic and urea and is between 3-5Moh depending on the application.
- It can be recycled and used multiple times, reducing waste generation.
Stainless Steel shot
- Steel shot is typically used for aggressive heavy-duty cleaning and surface preparation on tough materials.
- It is also a useful media for peening.
- Angular stainless steel, on the other hand, has a similar effect to aluminium oxide in that it has an effective cutting action.
- It is particularly useful for fast and efficient paint removal and preparation for coatings or treatments.
Ceramic beads / Zirconia
- Ceramic beads are also used for aggressive heavy-duty cleaning and surface preparation of tough materials.
- They can provide an even greater peening effect than stainless steel shot.
- And they are useful for the fast and efficient removal of paint and the preparation of surfaces for coatings or treatments.
Bauxite
- Bauxite is a relatively hard abrasive material, which makes it effective in removing tough coatings, corrosion, and surface contaminants. Its hardness allows for efficient surface cleaning and preparation.
- The sharp edges and hardness of bauxite particles enable it to cut through paint, rust, and other tough materials, making it suitable for applications that require strong abrasive action.
- Reusability: Bauxite can often be recycled and reused multiple times, reducing the overall consumption of abrasive media and lowering operational costs.
- It can be used for various wet blasting applications, including paint removal, surface preparation, cleaning, and deburring, in industries such as aerospace, automotive, marine, and construction.
- Bauxite abrasives are less likely to embed in the blasted surface, reducing the need for extensive cleanup after blasting.
- It is a naturally occurring non-toxic mineral and does not introduce harmful chemicals into the environment during wet blasting operations. This makes it an eco-friendly choice compared to some synthetic abrasive alternatives.
Many more abrasive media types are available, and that is before you consider the different mesh sizes, shape, hardness, density, toughness and blends of abrasive particles – which again have a significant impact on the surface finish produced, see below. The huge choice of different media types adds to the list of variables that make wet blasting more controllable than any other type of surface finishing process – helping to ensure the exact finish required can be achieved.
Size of abrasive media particles, measured in microns (µm), affects the roughness of the surface created, where larger particles create rougher surfaces and smaller particles create smoother surfaces.
Shape can have several different affects where round particles ‘hammer’ surfaces and angular particles ‘cut’ into surfaces.
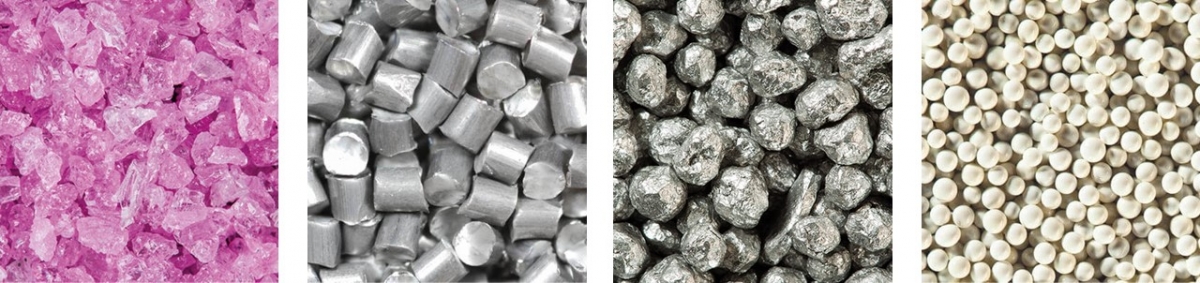
Angular, blocky, semi-round and spherical blast media
- Angular (cubic or elongated) gives a rough, matte finish
- Blocky (most edges flat) produces a dimpled surface
- Semi-round gives a smoother finish
- Spherical produces the smoothest finish of all and is also best for peening
Hardness affects cutting action and power, harder cuts better, while softer is better for cleaning. Typically measure in Moh’s numbers, the Moh hardness scale is not linear.
Mineral |
Moh’s No. |
Absolute hardness |
Talc |
1 |
1 |
Gypsum |
2 |
3 |
Calcite |
3 |
9 |
Fluorite |
4 |
21 |
Apatite |
5 |
48 |
Feldspar |
6 |
72 |
Quartz |
7 |
100 |
Topaz |
8 |
200 |
Corrundum |
9 |
400 |
Diamond |
10 |
1600 |
Density of abrasive affects the power of the blast: higher density equals higher power
Abrasive material |
Approx. densities (Kg/m3) |
Relative density to Alox |
Hardness (Moh) |
Steel |
8000 |
2.05 |
8-8.5 |
Aluminium oxide |
3900 |
1 |
9-9.2 |
Ceramic |
3850 |
0.98 |
9+ |
Glass beads |
2600 |
0.67 |
5-7 |
Plastic media |
1500 |
0.38 |
3.5 |
Toughness is an important consideration for recirculated abrasive systems at it affects the abrasive particles’ life. Brown aluminium oxide is tougher than pink, which is tougher than white. Glass beads can be made tougher by toughening processes and ceramic and stainless-steel shot are very tough and therefore last longer.
Blast media has a huge effect on surface roughness. As mentioned above, our ‘go-to’ blast media for producing a specific roughness is aluminium oxide. Roughness is measured in Ra, which is an average of the peaks and valleys of a surface finish (roughness average). Its units are microns, e.g. 20µm Ra. The surface roughness is important for certain applications, like the preparation of metal surfaces for painting or bonding. The size of the abrasive media particle affects the roughness of the finished surface, where the larger the particle the rougher the surface. The angle of the blast stream and air pressure can also have an effect on surface roughness.
For aesthetic finishing, use rounded media for a satin finish or sharp abrasive for a matte finish. Note that it is very difficult to produce a mirrored or highly polished finish with wet blasting alone. It is a finish that is better produced by post wet blasting processes. Glass beads or a mixture of glass beads and aluminium oxide are affective medias for aesthetic finishing.
We have vast experience of using all sorts of different media and it is typically the case that despite the huge variety, and thanks to all the other controllable variables associated with the wet blasting process, customers will generally opt for just two or three different types to achieve the precise finish they need.
The benefits of different wet blasting blast media lie in their cutting action, suitability for specific materials, reusability, environmental impact, and level of abrasiveness. Choosing the right media for a particular application ensures optimal results while minimising the risk of surface damage and waste generation.
We do not sell blast media directly but contact us and we will be more than happy to advise you on the best blast media for you particular application.